How Packaging Machine Repair Can Boost Your Production Output
How Packaging Machine Repair Can Boost Your Production Output
Blog Article
The Ultimate Overview to Product Packaging Equipment Repair: Keep Your Operations Running Smoothly
Recognizing the details of packaging device repair is critical for keeping ideal efficiency and decreasing interruptions. Regular upkeep not only expands the life of these makers but additionally addresses typical issues that can restrain efficiency.
Importance of Normal Maintenance
Normal maintenance of product packaging makers is essential for making certain ideal efficiency and durability. By implementing an organized maintenance routine, operators can determine potential problems prior to they intensify right into significant troubles. This proactive technique not only lessens downtime but likewise expands the lifespan of the tools, ultimately causing reduced operational prices.
Regular evaluations enable the assessment of important components such as seals, belts, and sensors. Addressing deterioration without delay prevents unforeseen failings that can disrupt production and cause pricey repairs. Additionally, routine upkeep aids make certain compliance with industry requirements and guidelines, cultivating a secure working environment.
Furthermore, maintenance activities such as cleaning, lubrication, and calibration substantially boost equipment performance. Boosted efficiency converts to regular item top quality, which is vital for maintaining customer satisfaction and brand reputation. A well-maintained packaging machine runs at optimum rates and lowers product waste, adding to total productivity.
Common Product Packaging Machine Concerns
Product packaging equipments, like any type of complicated machinery, can experience a variety of common concerns that may impede their performance and efficiency - packaging machine repair. One prevalent trouble is irregular sealing, which can lead to item wasting and waste if packages are not properly secured. This commonly results from misaligned components or used sealing elements
An additional regular issue is mechanical jams, which can take place because of foreign things, worn parts, or inappropriate positioning. Jams can cause hold-ups in production and rise downtime, eventually affecting general productivity. In addition, electronic breakdowns, such as failure in sensing units or control systems, can interrupt operations and lead to imprecise measurements or irregular device actions.
In addition, issues with item feed can also emerge, where items might not be delivered to the product packaging area constantly, causing disruptions. Wear and tear on rollers and belts can lead to suboptimal efficiency, needing prompt attention to avoid more damages.
Comprehending these typical concerns is vital for preserving the honesty of packaging operations, making sure that equipment runs smoothly and efficiently, which consequently aids in meeting production targets and preserving item top quality.
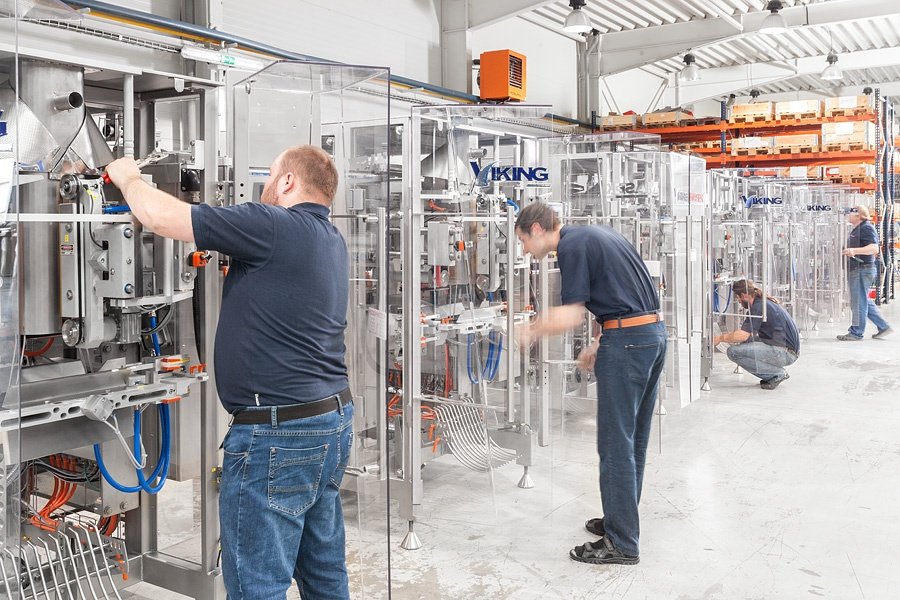
Repairing Methods
Effective repairing methods are vital for promptly resolving problems that occur with product packaging devices. A systematic strategy is important for identifying the origin cause of breakdowns and minimizing downtime. Begin by collecting information about the symptoms observed; this might include uncommon sounds, functional hold-ups, or mistake codes shown on the equipment's user interface.
Following, describe the equipment's guidebook for troubleshooting standards certain to the model in inquiry. This source can provide useful understandings into typical problems and recommended analysis steps. Use visual examinations to inspect for loosened links, worn belts, or misaligned parts, as these physical factors often contribute to operational failures.
Execute a procedure of elimination by screening specific equipment features. For instance, if a seal is not creating appropriately, evaluate the securing system and temperature level setups to determine if they meet operational specifications. Paper each step taken and the results observed, as this can aid in future repairing efforts.
Repair vs. Substitute Choices
When faced with devices great post to read malfunctions, deciding whether to repair or change a packaging equipment can be a complex and vital option. This decision rests on several vital variables, consisting of the age of the maker, the degree of the damage, and the projected influence on functional effectiveness.
First of all, consider the maker's age. Older machines might require even more frequent repair services, leading to higher advancing costs that can exceed the financial investment in a new device.
Operational downtime is one more crucial factor to consider. If repairing the maker will certainly cause long term delays, buying a brand-new device that uses enhanced effectiveness and integrity may be a lot more sensible. Think about the schedule of components; if substitute parts are hard to come by, it may be much more calculated to change the maker totally.
Inevitably, doing a cost-benefit analysis that consists of both prompt and long-lasting ramifications will aid in making an educated choice that straightens with your functional objectives and financial restrictions. (packaging machine repair)
Safety Nets for Durability

Secret safety nets include routine lubrication of moving parts, positioning checks, and calibration of sensing units and controls. Developing a cleansing timetable to remove debris and contaminants from machinery can substantially lower damage (packaging machine repair). In addition, keeping track of operational specifications such as temperature and vibration can assist discover abnormalities early
Educating personnel to identify indicators of wear or breakdown is an additional crucial component of preventive upkeep. Equipping operators with the understanding to perform basic troubleshooting can result in quicker resolutions and minimize operational disruptions.
Paperwork of maintenance activities, including solution documents and assessment findings, fosters accountability and facilitates educated decision-making pertaining to substitutes and repair work. By prioritizing preventative procedures, services can ensure their product packaging equipments operate at peak performance, inevitably causing enhanced productivity and lowered operational costs.
Verdict
Finally, the effective upkeep and repair work of packaging makers are critical for maintaining operational efficiency. Routine maintenance alleviates the risk of usual issues, such as irregular sealing and mechanical jams, while organized troubleshooting methods promote timely resolution of breakdowns. Mindful consideration of fixing versus replacement choices adds to affordable monitoring of resources. By executing safety nets, services can enhance device long life and ensure continuous performance in packaging operations.
Understanding the intricacies of packaging device repair service is vital for keeping optimum efficiency and decreasing disruptions.Regular maintenance of packaging machines is crucial for guaranteeing optimal performance and longevity.Packaging machines, like any intricate equipment, can run into a selection of usual problems that might impede their performance and efficiency. If fixing the equipment will certainly trigger extended delays, investing in a brand-new equipment that supplies improved performance and dependability might be extra prudent.In final thought, the effective maintenance and repair of packaging devices are critical for sustaining operational efficiency.
Report this page